Aluminum extrusions provide a great solution for industrial applications, offering an efficient and cost-effective way to maximize production. These versatile shapes are used in many different industries to improve performance and reduce costs.
With their light weight and strength, aluminum extrusions can be tailored to fit almost any application. From aerospace components to automotive parts and more, aluminum extrusions offer a variety of advantages that make them ideal for industrial use.
In this article, we will explore the benefits of using aluminum extrusion in industrial applications as well as how it can help save time and money while maximizing efficiency.
Benefits of Utilizing Aluminum Extrusions in Industrial Applications

Aluminum extrusions offer a wide range of advantages to industrial applications, significantly increasing efficiency and reducing costs. By utilizing aluminum extrusions in their operations, businesses can benefit from improved productivity through reduced downtime due to fewer repairs and maintenance requirements.
Moreover, the lightweight yet durable nature of aluminum makes it ideal for fast-paced production lines where speed is essential. Furthermore, its corrosion resistance ensures that parts remain in optimal condition over time with minimal need for replacement or repair.
The use of aluminum extrusions also allows businesses to save money on materials costs by requiring less material than other alternatives while still meeting performance needs. Additionally, businesses may be able to cut labor costs associated with installation and fabrication since extruded components are designed for easy assembly and integration into systems.
As a bonus, since aluminum is 100% recyclable, companies can reduce waste while taking advantage of cost savings associated with reusing or repurposing scrap metal into new products. Overall, integrating aluminum extrusions into industrial operations has proven itself beneficial both financially and operationally – creating greater efficiencies across the board without sacrificing quality or reliability.
Techniques to Increase Efficiency and Reduce Costs with Aluminum Extrusions
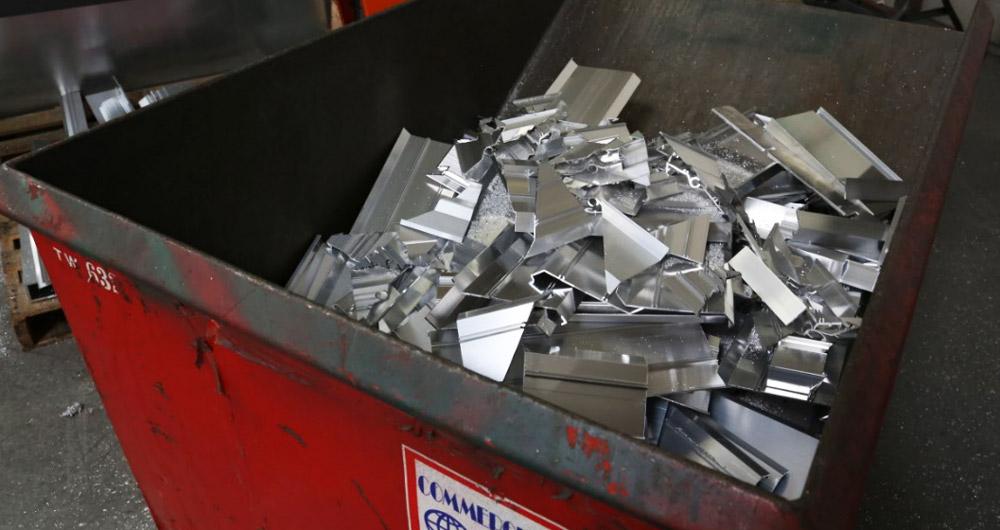
Aluminum extrusions offer an array of advantages to industrial applications, such as increased efficiency and cost savings. When it comes to maximizing these benefits, there are several techniques that manufacturers should consider.
Firstly, implementing a streamlined production process can help reduce costs associated with manufacturing aluminum extrusions. Automation is one way of achieving this – using automated equipment for tasks such as cutting and bending will minimize material waste and labor costs.
Additionally, utilizing high-quality raw materials and optimizing the extrusion design can also result in significant cost savings over time. Another way of increasing the efficiency of aluminum extrusions is by using advanced cooling systems during the post-extrusion process.
This helps reduce energy consumption while ensuring that the end product meets quality standards. In addition, applying heat treatment or surface treatments can improve both strength and durability while reducing production timescales considerably.
Finally, manufacturers should look into investing in advanced software solutions which streamline processes like quoting through to delivery tracking with greater accuracy than manual methods provide; allowing them to better manage resources more efficiently throughout their supply chain network resulting in reduced costs overall due to improved productivity levels at all stages of production.
Advantages of Using Aluminum Extrusions over Other Materials
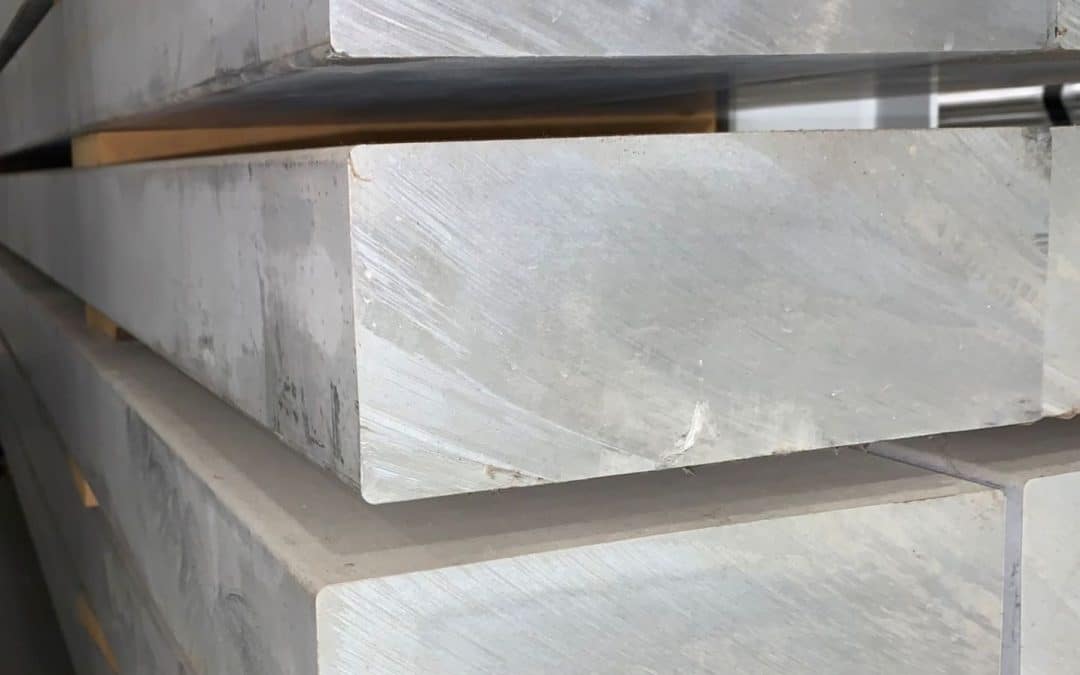
Aluminum extrusions offer numerous advantages when used in industrial applications. As a lightweight material, aluminum is easy to transport and install and can be shaped into almost any size or shape for an array of uses.
Aluminum is also highly resistant to corrosion, making it an ideal choice for use in harsh environments where other materials may not stand up well. When compared with other metals such as steel or iron, aluminum offers a superior strength-to-weight ratio which makes it much easier to handle during installation.
Additionally, aluminum extrusions can be cut or adapted easily on the job site allowing maximum flexibility throughout the project timeline. This helps speed up production time while minimizing costs associated with waste due to inaccurate measurements on prefabricated parts that are too large or small for the desired application.
In terms of sustainability and environmental benefits, aluminum has been proven to last longer than many other materials while requiring less energy during manufacturing processes resulting in lower emissions of carbon dioxide and fewer pollutants being released into the atmosphere overall. Finally, due to its low cost compared with some competing metals like titanium alloys, aluminum extrusion provides a great value proposition without sacrificing quality over time – ensuring customers get what they pay for without having to worry about long-term maintenance costs down the line.
Strategies to Maximize the Potential of Aluminum Extrusion Solutions in the Industry
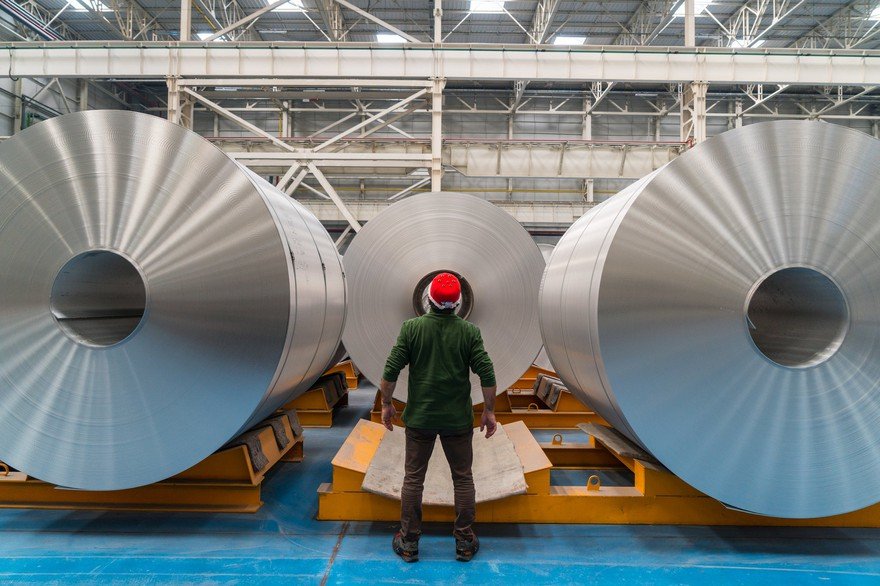
Aluminum extrusion solutions offer a wide range of opportunities for industrial applications to maximize efficiency and cost savings. For businesses, understanding the potential of aluminum extrusions is key to unlocking these benefits.
Here are some strategies that can help make sure youre maximizing the potential of your aluminum extrusions: 1) Identify Your Needs – Before investing in an aluminum extrusion solution, it\’s important to accurately assess your needs. Consider what type of product or service you need from your extrusion supplier and how much time and energy you\’ll have to devote to managing the project during installation.
2) Investigate Extrusion Profiles – Take full advantage of all the different shapes available with aluminum extrusions by researching which profiles will best suit the needs of your application. This could include T-slots, C-channels, U-channels, H-sections, tubes, or more complex designs such as special angles or curves depending on what works best for your company’s requirements.
3) Utilize Design Resources – Make use of design resources offered by suppliers that allow customers to customize their own extruded parts with easy online tools like CAD software packages so they can create precisely what they want without extensive outlay in terms of money and time. Doing this will also ensure any unique aspects required for a particular job are taken into account when creating a custom profile design specific to that purpose.
4) Understand Cost Savings Benefits – Aluminum extrusions come with many advantages including reduced manufacturing costs due to lower waste rates compared with other construction materials like steel or wood finish aluminum; plus increased speed since products arrive performed rather than needing cutting and assembly before being used in projects; along with lighter weight resulting in easier transportability between sites if necessary too! All these factors enable users to save both money as well as valuable time when dealing with various industries such as aerospace engineering where intricate details require precise measurements and facing tight deadlines at times! 5) Choose Experienced Suppliers – Choosing experienced suppliers who understand their customer’s needs is essential when selecting an appropriate provider for aluminum extrusion services– look out for companies who have been operating within the industry successfully over a long period providing quality assurance throughout production processes ensuring minimal defects occur upon completion!.
Conclusion

Aluminum extrusions are a great way to maximize efficiency and cost savings in industrial applications. They provide superior strength, durability, and design flexibility compared to other materials, making them ideal for use in construction and manufacturing.
Aluminum seamless tubes can be used as an efficient alternative to meet the needs of many industries due to their lightweight, high corrosion resistance, and ability to hold tight tolerances while still providing excellent strength-to-weight ratios. The low maintenance requirements of aluminum also make it a perfect choice for long-term projects.
Ultimately, when it comes time to maximize efficiency and cost savings in industrial applications, aluminum extrusions should always be the material of choice.